Greatest Guide to Metal Stamping Techniques and Applications
Greatest Guide to Metal Stamping Techniques and Applications
Blog Article
Optimizing Efficiency and Quality With Cutting-Edge Steel Stamping Techniques
In the world of metal marking, the pursuit of functional quality with the assimilation of innovative strategies is extremely important. As markets evolve and demands for precision and performance boost, remaining in advance of the curve becomes a calculated vital. By embracing cutting-edge technologies and process improvements, companies can open brand-new degrees of productivity and item quality. The junction of advanced steel marking methodologies, automated systems, strict quality assurance, and lean manufacturing concepts supplies a tantalizing look into the future of manufacturing. This convergence holds the guarantee of not just conference however going beyond sector criteria, establishing the stage for exceptional efficiency and customer satisfaction.
Advanced Steel Stamping Technologies
In the world of steel marking, the assimilation of sophisticated innovations has actually changed the industry, boosting precision and performance in making processes - Metal Stamping. Advanced metal marking technologies have played a crucial function in elevating the capabilities of producers, permitting for even more elaborate styles and higher production rates
One of one of the most substantial improvements in metal stamping modern technology is the implementation of computer system mathematical control (CNC) systems. CNC systems enable accurate control over the marking process, leading to precise and constant manufacturing of complicated components. Additionally, making use of servo presses has actually brought around enhancements in energy performance and decreased cycle times, further optimizing the production process.
Furthermore, the assimilation of automation and robotics has streamlined metal marking operations by increasing productivity and decreasing the threat of mistakes. Automated systems can carry out jobs with rate and accuracy, bring about boosted total performance in the assembly line.
Automated Processes for Efficiency
Usage of automated processes in steel marking procedures has substantially enhanced efficiency and productivity in making centers (Metal Stamping). Automated systems have actually reinvented the steel marking industry by streamlining processes, lowering hands-on treatment, and decreasing the margin of error. These automated options include a variety of technologies, including robot arms, CNC makers, and electronic control systems, that job cohesively to execute intricate marking tasks with precision and speed
One key advantage of automated processes in steel marking is the regular high quality they deliver. By getting rid of human mistake and variants in production, automated systems make sure that each stamped part fulfills specific specs with very little flaws. Automation allows continual operation, significantly minimizing downtime for device modifications and maintenance, therefore maximizing general efficiency.
In addition, automated procedures improve safety in steel stamping operations by lessening the demand for hand-operated handling of hefty materials and sharp tools. This not just safeguards workers but likewise adds to a more streamlined and effective operations. In conclusion, the assimilation of automated procedures in steel stamping procedures is important for attaining optimum effectiveness, top quality, and safety criteria in modern-day manufacturing atmospheres.
High Quality Control Measures in Stamping
Given the emphasis on regular quality and performance attained via automated procedures in metal stamping procedures, implementing robust quality control procedures comes to be necessary to make sure and maintain requirements accuracy in stamped components. Quality assurance in steel stamping website here entails a multi-faceted strategy to assure the dependability and accuracy of the final items. Inspection checkpoints at different phases of the marking process are important to identify any discrepancies from specifications early on. Utilizing sophisticated technologies such as computerized vision systems and automated dimension devices can boost the rate and precision of high quality evaluations. Analytical procedure control approaches aid in monitoring and managing the stamping procedure to find any variants that might impact quality. In addition, training programs for team on high quality requirements and procedures are critical to ensure that every person entailed comprehends and adheres to the well established high quality control methods. By integrating these procedures into steel stamping procedures, producers can regularly produce top notch stamped parts that satisfy the strict demands of modern-day industries.
Enhancing Accuracy Through Technology
To achieve unequaled accuracy in steel marking procedures, pioneering advancements are constantly being developed and integrated right into the manufacturing process. Advanced technologies such as laser cutting systems and computer system mathematical control (CNC) devices have actually transformed the way steel parts are marked with utmost precision. By using laser reducing click resources innovation, manufacturers can attain intricate and detailed designs with micron-level precision, ensuring that each stamped component fulfills the strictest top quality criteria.
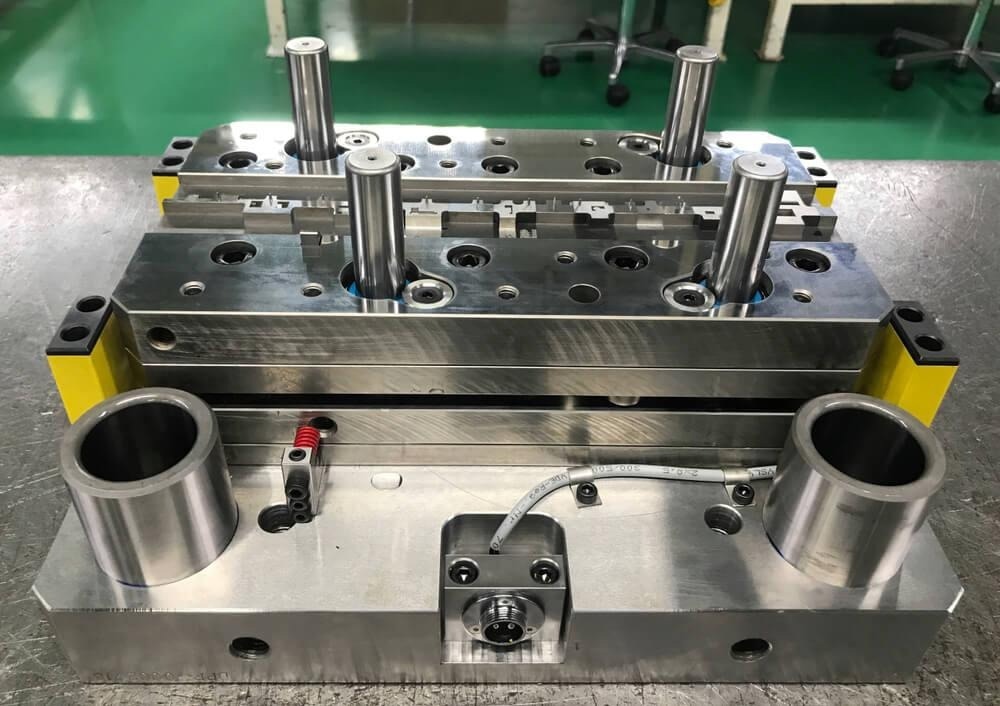
Additionally, using simulation software program allows manufacturers to assess and maximize stamping procedures prior to real manufacturing, identifying potential locations for enhancement and make improvements criteria to accomplish optimum precision. By accepting these innovative innovations, suppliers can boost accuracy, increase efficiency, and her response deliver top quality stamped items that fulfill the most rigid needs of contemporary markets.
Executing Lean Production Practices
Including lean production practices right into steel stamping procedures can lead to streamlined production procedures and raised overall efficiency. By focusing on removing waste, maximizing resources, and constantly boosting procedures, metal stamping companies can improve efficiency and top quality while decreasing prices.
Additionally, lean production techniques urge a culture of continual improvement within the company. By encouraging employees to recognize and attend to inadequacies, business can make step-by-step modifications that lead to substantial efficiency gains in time. Executing tools such as five, Kanban systems, and value stream mapping can assist streamline procedures, lower lead times, and boost overall quality in metal stamping processes.
Verdict
Finally, the utilization of advanced steel marking technologies, automated procedures, quality assurance steps, technology for accuracy enhancement, and execution of lean production methods are crucial for taking full advantage of performance and top quality in metal marking operations. These methods make certain that items are created with cost-effectiveness, uniformity, and accuracy. By incorporating these cutting-edge techniques, manufacturers can remain affordable in the sector and satisfy the demands of clients effectively.
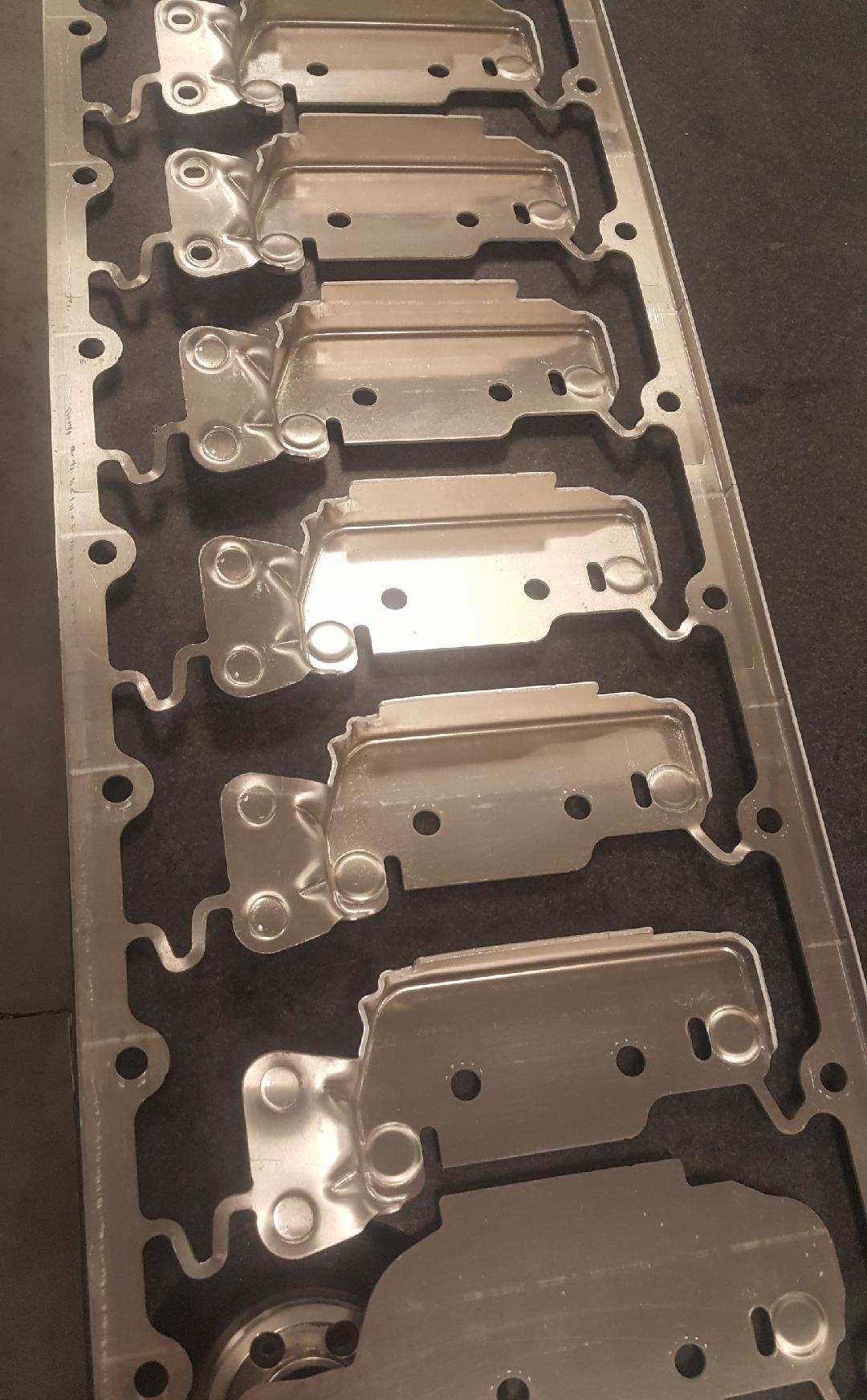
Provided the emphasis on consistent high quality and effectiveness achieved with automated processes in steel marking operations, applying durable quality control measures comes to be necessary to support requirements and make sure accuracy in stamped parts. Executing tools such as 5S, Kanban systems, and worth stream mapping can assist enhance procedures, minimize lead times, and enhance general high quality in metal stamping procedures.
In conclusion, the usage of sophisticated steel marking technologies, automated processes, high quality control measures, development for accuracy enhancement, and implementation of lean manufacturing practices are essential for making best use of effectiveness and quality in metal stamping operations.
Report this page